TDG Regulations :
10 questions to take stock !
- What are the dangerous goods concerned by the TDG regulations ?
- What regulations apply to the transportation of dangerous goods?
- Which companies must designate a Safety Advisor for the Transportation of Dangerous Goods (STEM)?
- What is the role of the Transportation of Dangerous Goods Safety Advisor (TDSA)?
- Who can be a TDSP?
- What are the TDG obligations related to personnel training?*
- When is it necessary to use an approved packaging ?
- Where can I find an approved packaging ?
- What is the approval procedure for a packaging and what tests are performed ?
- When are lithium batteries considered dangerous goods?
You can't find an answer to your question? Ask one of our experts directly!
1 - What are the dangerous goods concerned by the TDG regulations ?
The dangerous goods concerned by the regulation are the following :
- Explosive substances and articles (Class 1)
- Gases (Class 2)
- Flammable liquids (Class 3)
- Flammable solids, self-reactive substances, desensitized explosive solids and substances which polymerize (Class 4.1)
- Substances liable to spontaneous combustion (Class 4.2)
- Substances which, in contact with water, emit flammable gases (Class 4.3)
- Oxidizing substances (Class 5.1)
- Organic peroxides (Class 5.2)
- Toxic substances (Class 6.1)
- Infectious substances (Class 6.2)
- Radioactive materials (Class 7)
- Corrosive substances (Class 8)
- Miscellaneous dangerous substances and objects (Class 9)
2 - What regulations apply to the transportation of dangerous goods?
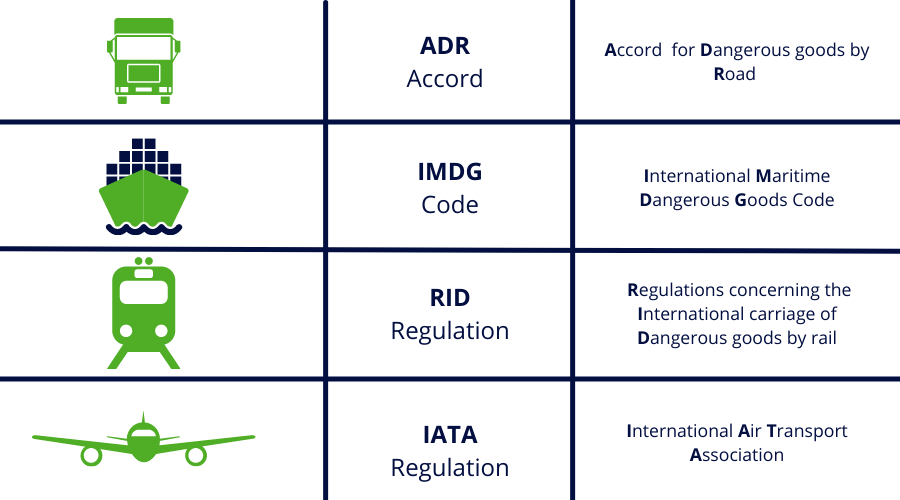
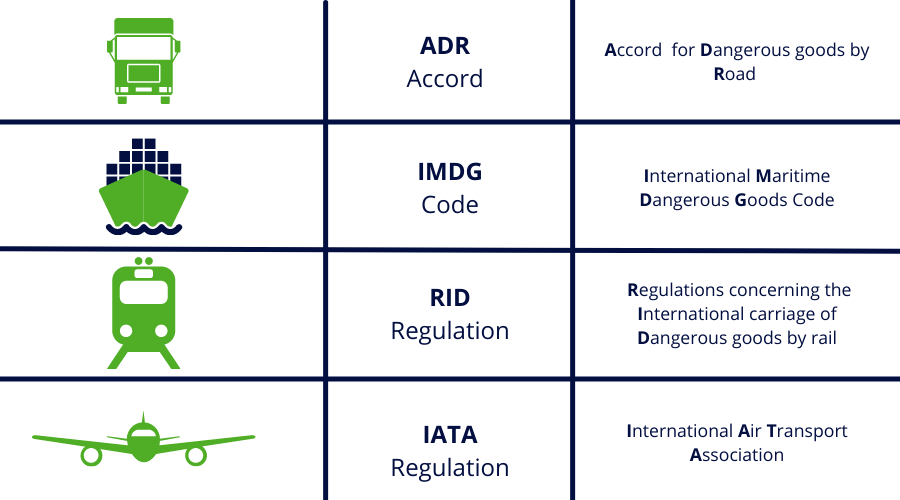
The regulations are based on different international regulations, in order to allow the circulation of dangerous goods between the countries concerned.
Several reference texts exist, depending on the transport methods used :
- ADR
- IMDG
- IATA
- RID
- ADN
In France, these international regulations concerning TDG by land (ADR/RID/ADN) are implemented by the modified decree of May 29, 2009 (known as the "TDG decree") concerning the transport of dangerous goods by land.
3 - Which companies must designate a Safety Advisor for the Transportation of Dangerous Goods (STEM)?
Since 2001, any company that loads, packages, transports or unloads hazardous materials has been required to employ the services of one or more Hazardous Materials Transportation Safety Advisors (HMTSAs). Since 2019, this obligation has been extended to all companies that ship dangerous goods, even if they do not physically carry out the operations. This also applies to principals, but also to companies working as forwarding agents, transport agents and retail chains. A transitional phase is planned for these companies until 31 December 2022.
The objective of the designation of the CSTMD is to prevent risks to people, goods and the environment.
From January 1, 2021, the declaration of the CSTMD, whether internal or external, will be facilitated and must be done online (teledeclaration) on the internet portal set up by the Ministry of Ecological and Solidarity Transition. This remote declaration service is already operational.
Companies that already have a CSTMD are of course also concerned and will have to register it online.
4 - What is the role of the Transportation of Dangerous Goods Safety Advisor (TDSA)?
The role of the Safety Advisor for the Transport of Dangerous Goods (TDGSA) is to :
- Ensure compliance with the rules relating to the transportation, packaging, shipping, loading and unloading of dangerous goods.
- Analyze and advise the company on its practices and procedures related to the loading, unloading, packaging and transportation of dangerous goods.
Before March 31 of each year, the DGHWC is required to prepare an annual report, which includes a description of its activities for the past year. This report is based on one or more visits to the company. This report must be kept by the company for 5 years.
He must also write a report in case of an incident or accident during a loading, transport or unloading operation, to be sent to the relevant administration.
5 - Who can be a TDGSA ?
The safety advisor may be internal to the company or external.
In all cases, he must hold a certificate issued by the CIFMD (Interprofessional Committee for the Development of Training in the Transport of Dangerous Goods) and the company must declare its CSTMD to the DREAL.
6 - What are the TDG obligations related to personnel training?
All persons involved in the transport chain of dangerous goods (handling, packaging, storage, unloading and transport) must be specifically trained.
7 - When is it necessary to use an approved packaging ?
You are a shipper of goods classified as dangerous by the regulations, such as perfumery products, glues and varnishes, lithium batteries, etc. The packaging you use must be adapted to the goods you are going to ship and be approved accordingly according to the chosen mode(s) of transport.
Several types of packaging are concerned by these regulations: cartons, drums, bags, IBCs (Intermediate Bulk Containers)... each of which has specific requirements that will allow your packages to arrive safely at the other end of the world.
8 - Where can I find an approved packaging ?
Each type of packaging has its own certificate of approval, which may be held by the manufacturer of the packaging or, in some cases, by the shipper.
It will therefore be necessary for you to either:
- Obtain the approved packaging from the manufacturer,
- Obtain the approval yourself for packaging manufactured by a supplier you have chosen.
In all cases, an organization approved by the ministry in charge of transporting dangerous goods is the only one authorized to test the packaging and issue these approvals.
9 - What is the approval procedure for a packaging and what tests are performed?
Approval consists in carrying out mechanical and/or chemical tests :
- Mechanical tests are used to determine the resistance of the packaging in the event of an accident or incident during the loading, unloading and transport phases. Depending on the packaging, they include drop, air-tightness, hydraulic pressure, stacking and vibration tests.
- The chemical compatibility tests concern plastic packaging intended to contain liquids. They consist in performing mechanical tests on packagings previously aged with reference liquids defined in the ADR regulations or with the actual products to be transported.
Once the tests are completed, a test report is submitted. If the tests are successful, a certificate of approval is also issued.
10 - When are lithium batteries considered as dangerous goods?
The ADR regulation applies when the nominal energy of a lithium ion cell exceeds 20 Wh and when the nominal energy of a lithium ion battery exceeds 100 Wh.